Основы Теории Листовой Штамповки 6,9/10 7224reviews
Основы теории технологических процессов листовой, объемной штамповки, ковки. Разделительные операции. Резка листового металла на ножницах. Для холодной листовой штамповки листовые металлы с помощью ножниц предварительно разрезают на заготовки необходимых размеров. Основными типами ножниц (рис.
Первый тип ножниц используется для резки узких и толстых полос и неметаллов. Ножницы с наклонными ножами (гильотинные) - для резки металлических листов. Для резки рулонного металла и обрезки кромок лент применяют дисковые ножницы. Вибрационные ножницы для получения штучных заготовок криволинейной формы. В процессе резки (рис.
S0, подвергается воздействию верхнего и нижнего ножей, при этом на заготовку действует сила P. Под действием момента, образованного парой сил, заготовка начинает поворачиваться и давит на боковую поверхность ножей, вследствие чего возникает сила бокового давления Т. Верхний нож, внедряясь в заготовку на величину h, вызывает появление скалывающих трещин, направленных под углом 0.
При правильно выбранной величине зазора z=(0,0. S0 скалывающие трещины со стороны верхнего и нижнего ножей совпадают, образуя поверхность разделения.

Величину внедрения ножей можно определить по формуле h=y. S0, где у=F0/Fm - величина относительного сужения, найденная из опытов на растяжение; F0, Fm - соответственно, начальная площадь и площадь поперечного сечения образца в момент образования шейки.
Глубина внедрения h до появления трещин колеблется от 0,1 до 0,5 толщины заготовки, увеличиваясь с увеличением пластичности металла. При резке выделяют три основные стадии процесса: упругих деформаций, пластических деформаций и скалывания. Продолжительность стадий зависит от пластичности штампуемого металла, состояния поверхности инструмента и скорости деформации. В соответствии с этими стадиями происходит изменение силы деформации Р (рис. Н: на первой стадии - медленное нарастание силы (смятие и образование очага деформации); на второй - значительный рост (сдвиговая деформация) до максимального значения; на третьей - быстрое падение силы вследствие скола. Анализируя соответствующие графики для различных типов ножниц (рис. В табл. 1. 1 приведены формулы для расчета энергосиловых параметров (силы P, работы деформации A и крутящего момента M) при резке металла на различных типах ножниц.
Описаны рациональные технологнческие процессы многопозиционной листовой штамповки деталей, Даны основы теории устойчивости процесса . Сторожев М.В., Попов Е.А. Название: Основы теории листовой штамповки. Автор: Попов Е.А. Издательство: Машиностроение Год: 1968. Формат: djvu. Обработка металлов давлением — технологический процесс получения заготовок или. Листовой штамповкой получают плоские и пространственные полые детали из заготовок, у которых.
Здесь к = 1,0.. 1,3 - коэффициент, учитывающий условия резки, X - коэффициент, зависящий от рода и толщины металла, X = 0,3- 0,7. Резка листового металла штампами. Основными операциями резания металла штампами являются вырубка и пробивка.
Попов Е.а Основы Теории Листовой Штамповки


Данные процессы можно представить в виде отделения одной части заготовки от другой по замкнутому контуру с помощью пуансона и матрицы (рис. При вырубке часть заготовки, которая остается на матрице, является отходом, а при пробивке та же часть заготовки является деталью.
Для холодной листовой штамповки листовые металлы с помощью ножниц предварительно разрезают на заготовки необходимых размеров. Сплавных формообразующих деталей штампов. Знание основ теории листовой штамповки помогает современному специалисту в области обработки . Листовая штамповка — листовое штампование, изготовление полуфабрикатов, деталей и готовых изделий из листовых металлических заготовок . Основы проектирования технологических операций холодной.
Так же, как и при резке ножницами, процесс резки состоит из трех стадий: упругой, пластической и скалывания. При этом последовательно происходит упругий изгиб с вдавливанием по кольцевому пояску со стороны матрицы и пуансона, возникновение изгибающего момента (выпучивание) и образование трещин со стороны матрицы и пуансона. Особенностью напряженно- деформированного состояния является различие схем напряженно- деформированного состояния в различных частях деформируемой заготовки (рис. Непосредственно под режущей кромкой пуансона создается напряженное состояние объемного сжатия, а над режущей кромкой матрицы - напряженное состояние с напряжениями радиального растяжения. Первое более благоприятно для пластического течения металла, а второе - менее благоприятно и способствует возникновению микротрещин в зоне резания. В центральной части заготовки схема напряженного состояния плоская и отсутствуют осевые сжимающие напряжения. Большое влияние на деформацию металла и энергосиловые параметры оказывает выбор зазора z.
При оптимальном зазоре z=(5 - 1. S0 поверхности сдвига и трещины со стороны пуансона совпадают с соответствующими трещинами со стороны матрицы. При малом зазоре и большой толщине металла от несовпадения трещин образуется кольцевая перемычка, которая перерезается с возникновением новых скалывающих трещин, и на детали образуется надрыв и двойной срез с протянутым заусенцем.
В случае очень большого зазора на поверхности образуются рваные заусенцы от затягивания и обрыва металла в зазоре. Полное сила деформации при вырубке (пробивке) может быть рассчитано по формуле. P=k. Различают одноугловую, двухугловую, многоугловую гибку, закатку и завивку (рис. При одноугловой гибке слои металла внутри угла изгиба (со стороны пуансона) сжимаются и укорачиваются в продольном и растягиваются в поперечном направлении (рис. Наружные слои (со стороны матрицы) растягиваются и удлиняются в продольном и сжимаются в поперечном направлениях. Между удлиненными и укороченными слоями находится нейтральный слой (н.
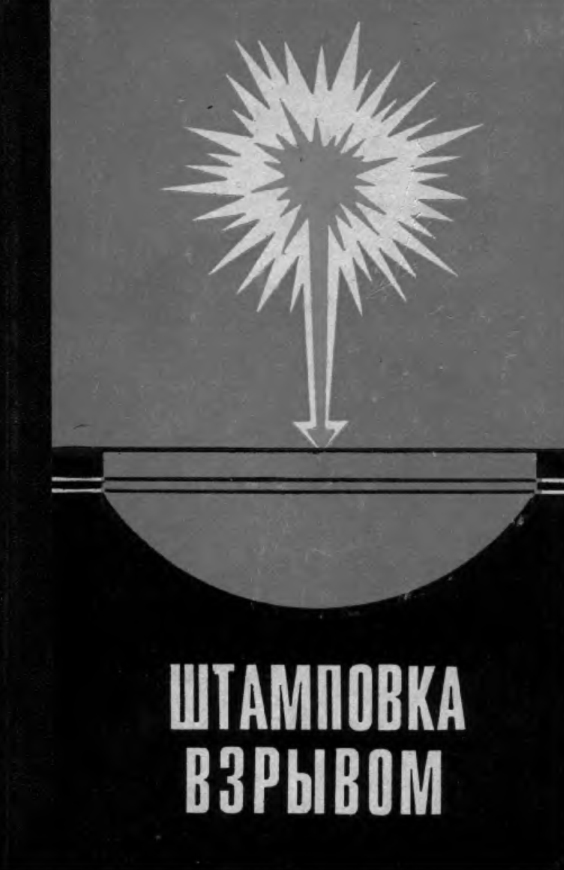

Радиус нейтрального слоя можно определить по формуле. При этом происходит постепенное уменьшение радиуса кривизны и плеча изгиба (L1,L2,LK). Немаловажными величинами, определяющими возможность осуществления листовой гибки, являются минимально допустимые радиусы гибки. Они должны соответствовать пластическим свойствам металла и не допускать образования трещин. Вытяжка. Вытяжка - это технологическая операция ЛШ, заключающаяся в превращении плоской или полой заготовки в открытое сверху полое изделие замкнутого контура. По геометрической форме получаемых деталей выделяют вытяжку изделий осесимметричной, коробчатой и сложной несимметричной формы.
Кроме того, различают вытяжку с прижимом и без прижима, а также с утонением и без утонения стенок. Схема вытяжки без прижима приведена на рис. Пуансон, воздействуя на центральную часть заготовки (рис. Дальнейшее опускание пуансона приводит к появлению радиальных растягивающих напряжений, достаточных для перевода фланцевой части заготовки в пластическое состояние. С этого момента начинается втягивание заготовки в матрицу с образованием боковых поверхностей вытягиваемого изделия при одновременном уменьшении диаметра заготовки. Действие радиальных растягивающих напряжений .
Совместное действие этих напряжений обеспечивает втягивание фланца в отверстие матрицы и получение изделия (рис. За одну операцию вытяжки можно получить одну неглубокую деталь, т. Сечение 1. Фланцевая часть находится под воздействием тангенциальных и осевых сжимающих напряжений и радиального растягивающего, то есть реализуется объемная схема напряженного и деформированного состояния.
Без прижима осевые напряжения . Для предотвращения этого явления используется прижим или складкодержатель, при применении которого осевая деформация . В данном сечении перехода от фланца к цилиндрической части изделия реализуется сложная деформация, вызванная пространственным изгибом, наибольшим радиальным растяжением и незначительным тангенциальным сжатием. Действующие в этом сечении радиальные растягивающие напряжения являются максимальными и могут привести к отрыву фланцевой части заготовки, особенно при большой величине силы прижима Q.
Сечение 3. В стенке (цилиндрической части) полого изделия реализуется линейно- напряженное и плоско- деформированное состояние. Сечение 4. Часть данного закругления изделия является наиболее опасным с точки зрения возникновения трещин сечением.
Это вызвано действием объемной схемы напряжений двухосного растяжения и одноосного сжатия, под действием которых происходит значительное утонение стенок в этой части заготовки. Для предотвращения отрыва дна от стенок, что является следствием действия такой схемы н.
Обработка металлов давлением — Википедия. Ковка — один из видов обработки металлов давлением. Обработка металлов давлением — технологический процесс получения заготовок или деталей в результате силового воздействия инструмента на обрабатываемый материал. Процессы обработки металлов давлением по назначению подразделяют на два вида: для получения заготовок постоянного поперечного сечения по длине (прутков, проволоки, лент, листов), применяемых в строительных конструкциях или в качестве заготовок для последующего изготовления из них деталей — только обработкой резанием или с использованием предварительного пластического формоизменения, основными разновидностями таких процессов являются прокатка, прессование и волочение; для получения деталей или заготовок (полуфабрикатов), имеющих приближённо формы и размеры готовых деталей и требующих обработки резанием лишь для придания им окончательных размеров и получения поверхности заданного качества; основными разновидностями таких процессов являются ковка и штамповка. Прокатка — процесс пластического деформирования тел между вращающимися приводными валиками.
Прессование заключается в продавливании заготовки, находящейся в замкнутой форме, через отверстие матрицы, причём форма и размеры поперечного сечения выдавленной части заготовки соответствуют форме и размерам отверстия матрицы. Волочение заключается в протягивании заготовки через сужающуюся полость матрицы или через межвалковое пространство образованное двумя или более валками; площадь поперечного сечения заготовки уменьшается и получает форму поперечного сечения отверстия матрицы. Ковкой изменяют форму и размеры заготовки путём последовательного воздействия универсальным инструментом на отдельные участки нагретой заготовки. Штамповкой изменяют форму и размеры заготовки с помощью специализированного инструмента — штампа (для каждой детали изготовляют свой штамп), который состоит из матрицы, пуансона и дополнительных частей. Различают объёмную и листовую штамповку.
При объёмной штамповке в качестве заготовки используют сортовой металл, разрезаемый на заготовки. На заготовку в процессе объемной штамповки воздействуют специализированным инструментом — пуансоном, при этом металл заполняет полость матрицы, приобретая её форму и размеры. Листовой штамповкой получают плоские и пространственные полые детали из заготовок, у которых толщина значительно меньше размеров в плане (лист, лента, полоса). Обычно заготовка деформируется с помощью пуансона и матрицы. Существуют также процессы, которые являются комбинациями из нескольких методов.
Например, метод прокатка- волочение, прокатка- прессование и т. Обработка металлов давлением основана на их способности в определенных условиях пластически деформироваться в результате воздействия на деформируемое тело (заготовку) внешних сил. Если при упругих деформациях деформируемое тело полностью восстанавливает исходные форму и размеры после снятия внешних сил, то при пластических деформациях изменение формы и размеров, вызванное действием внешних сил, сохраняется и после прекращения действия этих сил. Упругая деформация характеризуется смещением атомов относительно друг друга на величину, меньшую межатомных расстояний, и после снятия внешних сил атомы возвращаются в исходное положение.
При пластических деформациях атомы смещаются относительно друг друга на величины, больше межатомных расстояний, и после снятия внешних сил не возвращаются в своё исходное положение, а занимают новые положения равновесия. Игра Сталкер Львиное Сердце. Холодная штамповка как технология известна достаточно давно. Ещё в конце первого тысячелетия древнерусские мастера стали применять метод холодной штамповки для производства металлической посуды. Саму холодную штамповку отличает достаточно высокое качество получаемых изделий, высокая скорость их изготовления, а также низкая цена на само изделие — разумеется, как уже было отмечено, при массовом их производстве. Холодная штамповка заключается в механическом воздействии штампа в процессе прессования листов металла, итогом которого получаются готовые изделия. Таким образом, сам штамп выступает в роли технологической насадки для прессовального механизма, его можно использовать только для одной операции. Кроме того, операции холодной штамповки легко поддаются автоматизации, в том числе могут проводиться с помощью промышленных роботов, что способно сделать производство методом холодной штамповки ещё более выгодным.
Холодная штамповка технологически подразделяется на два основных вида. Первый — это операции разделительные. Наименование операции зависит от контура разделения. Если разделение происходит по незамкнутому контуру, это операции резки, если по замкнутому контуру: операции пробивки (различные отверстия) и вырубки (различные плоские детали, например, круглой формы в плане).
Второй тип операций — операции формоизменения: гибка, вытяжка, формовка, а если исходная заготовка труба — раздача и обжим. Иногда операции двух типов объединяют — например, производят одновременно вытяжку и рубку или гибку и обрезку. В таком случае применяются так называемые комбинированные штампы. Для операций холодной штамповки необходимо использовать металлы и сплавы, которые обладают гибкостью, пластичностью, а также дешевизной.